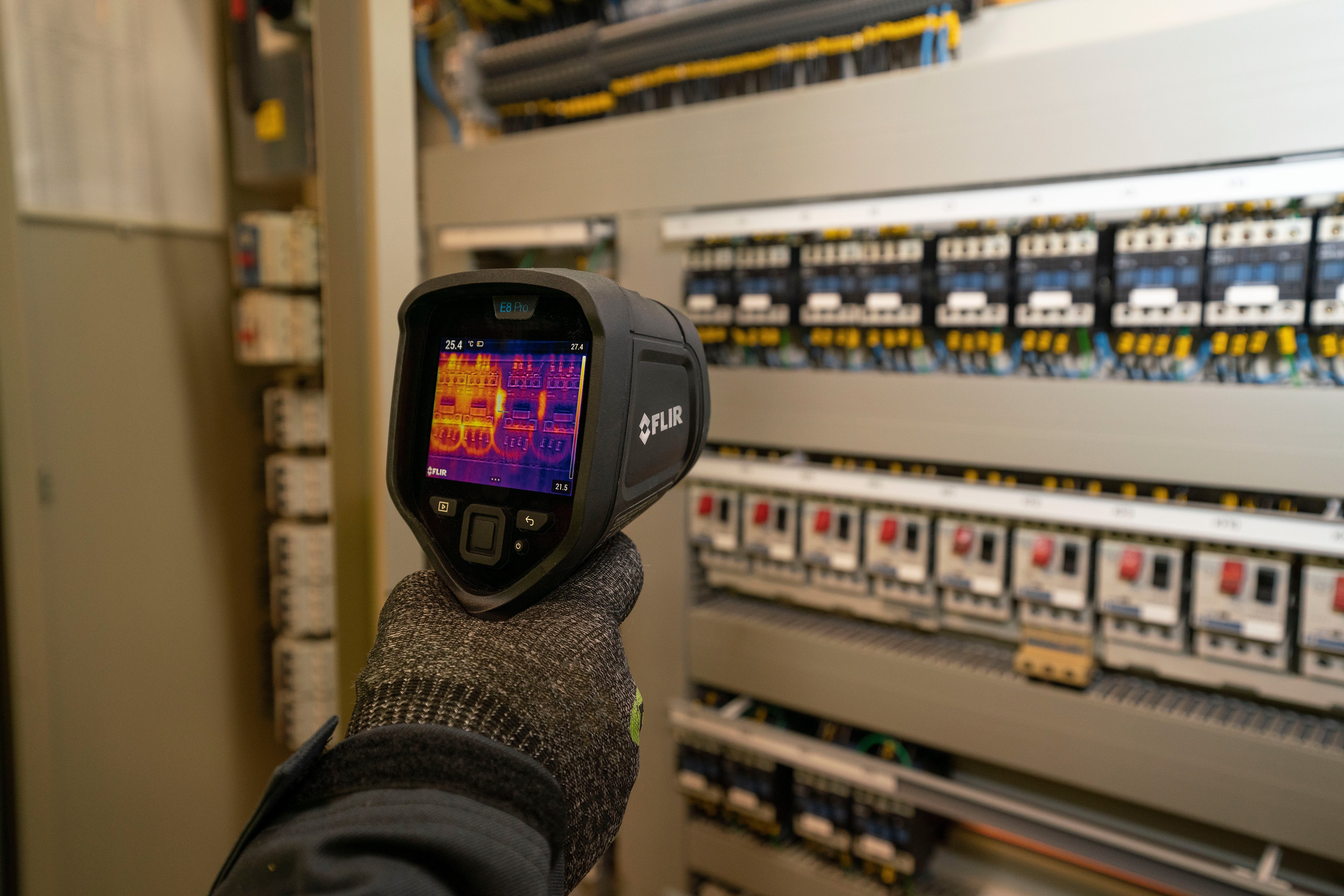
Electrical panel thermography services involve the use of infrared (IR) cameras to inspect electrical panels and components for any potential issues like overheating, poor connections, or faulty equipment. These issues often result in energy loss, equipment damage, or even fire hazards. The thermographic inspection is a non-invasive method that can detect temperature anomalies in electrical systems without disrupting normal operation.
Here’s a brief overview of what this service typically entails:
1. Inspection Process:
- Preparation: The electrical panel and surrounding area are examined for any visible signs of wear, corrosion, or damage.
- Thermal Imaging: A trained thermographer uses an infrared camera to scan the electrical components, looking for temperature variations that indicate potential faults like overloaded circuits, loose connections, or faulty breakers.
- Temperature Analysis: The thermographic camera captures infrared images (thermograms) that show temperature differences across various components. The technician then analyzes these to identify any hot spots that could indicate issues.
2. Common Issues Identified:
- Overloaded Circuits: High current can cause components to overheat, leading to failures or fires.
- Loose Connections: Poor connections or contact resistance can cause localized heating, which is easily detectable with thermal imaging.
- Failing Breakers: If a breaker is not functioning correctly, it might not trip as it should, causing temperature rise and possibly resulting in damage.
- Corroded or Damaged Wiring: Wires with insulation issues or corroded terminals might show abnormal temperature readings.
- Equipment Failures: Aging electrical equipment, like transformers, can show signs of overheating due to internal issues.
3. Reporting and Recommendations:
After the inspection, a detailed report is provided. This includes:
- Thermographic images showing temperature anomalies.
- Description of the issue identified, including potential risks.
- Recommendations for repairs or maintenance to resolve any identified problems.
4. Benefits of Thermography:
- Preventative Maintenance: Early detection of problems can prevent costly repairs or failures in the future.
- Minimized Downtime: The inspection is non-invasive, meaning no system shutdowns or interruptions are required.
- Safety: Reduces the risk of electrical fires and equipment damage by identifying hazards before they escalate.
5. Ideal Frequency for Inspections:
- Regular thermographic inspections are recommended annually or biannually, especially for older equipment or systems in high-demand environments.
Thermography is a powerful tool for keeping electrical systems running smoothly and safely.
ELectrical Thermography Inspection in Ras al Khaimah
Thermography Service in Ras al Khaimah